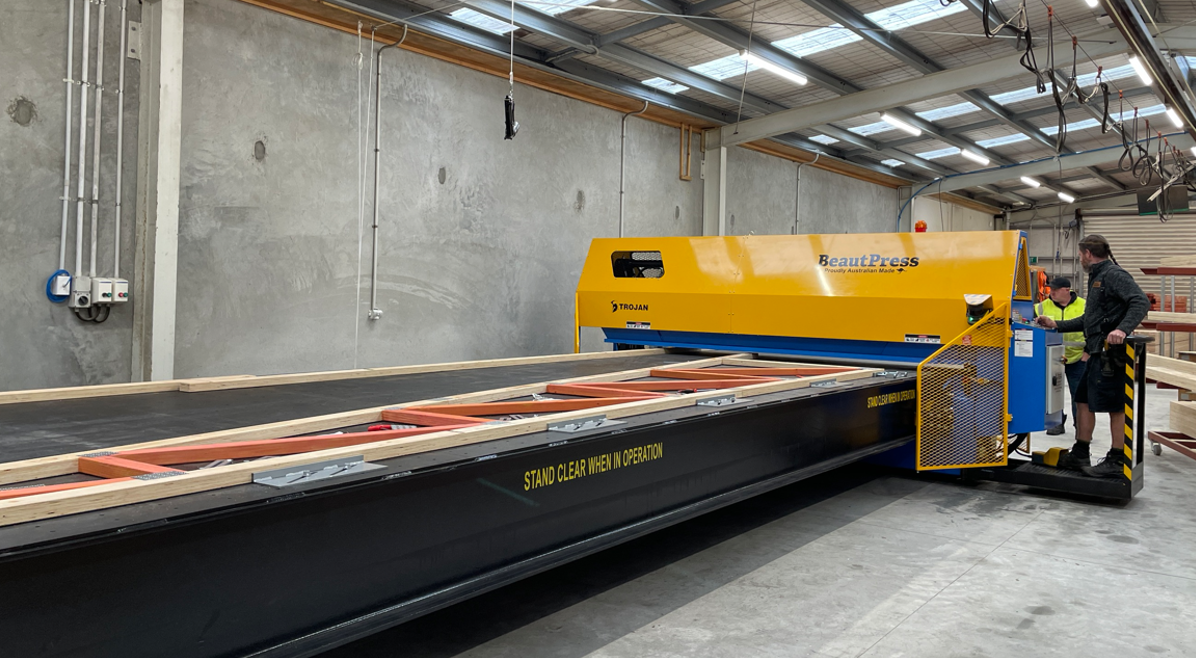
Griffen & Smith has been a cornerstone of the West Coast’s building supply industry for over 100 years. What began as a small retail hardware store has evolved significantly, particularly with its investment in frame and truss manufacturing. The company joined the Mitre 10 group in 1977, further cementing its role as a trusted supplier.
The Greymouth Truss Plant, part of Griffen & Smith, has seen its fair share of changes. Frame and truss manufacturing has been an on-and-off endeavour for the company, largely dependent on leadership and profitability. With limited competition on the West Coast and significant transport costs for builders sourcing from Christchurch, Nelson or Blenheim, Griffen & Smith recognised an opportunity to reinvest in the segment.
Simon Barber, Truss Plant Manager, explains, “The business saw a real opportunity to support local builders and save them considerable transport costs—up to $2,500 per trip from Christchurch alone. The demand was there, and we had the skills to make it work. It was just a matter of ensuring we had the right setup.”
Investing in the Right Technology
In mid-2023, the plant took a significant step forward with the installation of the MiTek BeautPress Trojan. The upgrade replaced an outdated gantry press and has since transformed operations.
“The speed of pressing has increased dramatically. Previously, we had to press each plate individually, which was time-consuming. Now, with the BeautPress, pressing is two to three times faster, depending on the truss design,” says Simon. “Setups are also quicker because the system ensures everything is built straight and accurately from the start.”
Beyond speed, the BeautPress has provided greater accuracy and efficiency. “We measure everything straight off the table, so setup times are significantly reduced. And because of the large work surface, we are also using it for framing—doing all our raking walls and window assemblies there, making the entire plant more efficient.”
Customisation for a Compact Plant
With only 300 square meters of space, the Greymouth Truss Plant faced unique constraints. MiTek tailored the BeautPress installation to fit within the facility’s limited footprint. “We looked at other options, but they just weren’t viable. The BeautPress allowed us to install a system that fit our space while still accommodating 3-meter-high frames—our maximum build size before transport restrictions kick in,” says Simon.
A key modification was the addition of a hinged operator platform, allowing space to be maximised when the press is not in use. “We worked directly with MiTek’s team, and within days they had a solution. That level of support made a huge difference.”
Safety and Support
The new system has also introduced significant safety improvements. Unlike the old gantry press, which had hydraulic hoses and heavy moving parts, the BeautPress has built-in containment and safety sensors that eliminate most risks. “The system’s lasers prevent anyone from getting too close whilst it is in operation. Even something as small as a water bottle left on a truss will trigger a stop,” Simon notes. “With the old system, if someone wasn’t paying attention, there was a real risk of injury. That’s no longer a concern.”
MiTek provided comprehensive support throughout the installation and beyond. “Once the deal was signed, we had constant updates on progress, shipping and delivery. When the install team arrived, they ensured everything was up and running smoothly. The ongoing support has been excellent,” says Simon.
The Future of Frame & Truss at Greymouth
The efficiency gains from the BeautPress have allowed Greymouth Truss Plant to take on more work and improve profitability. “Previously, trusses were the bottleneck. Now, we can push through more jobs quickly and focus on framing—where the real opportunity for growth is,” Simon explains.
With only two full-time staff and additional workers brought in as needed, the increased efficiency has been transformative. “Now, even with just two of us, we can keep up. When we bring in more hands, we really start moving,” says Simon. “It’s made a huge difference to what we can achieve.”
By investing in the right technology and working closely with MiTek to tailor a solution, Greymouth Truss Plant has positioned itself as a key player in the local market. Builders on the West Coast now have a reliable, cost-effective option for high-quality frame and truss products, produced faster and with greater precision than ever before.